Low-Cost Heat-Resistant Resin Molds for Low-Volume Production
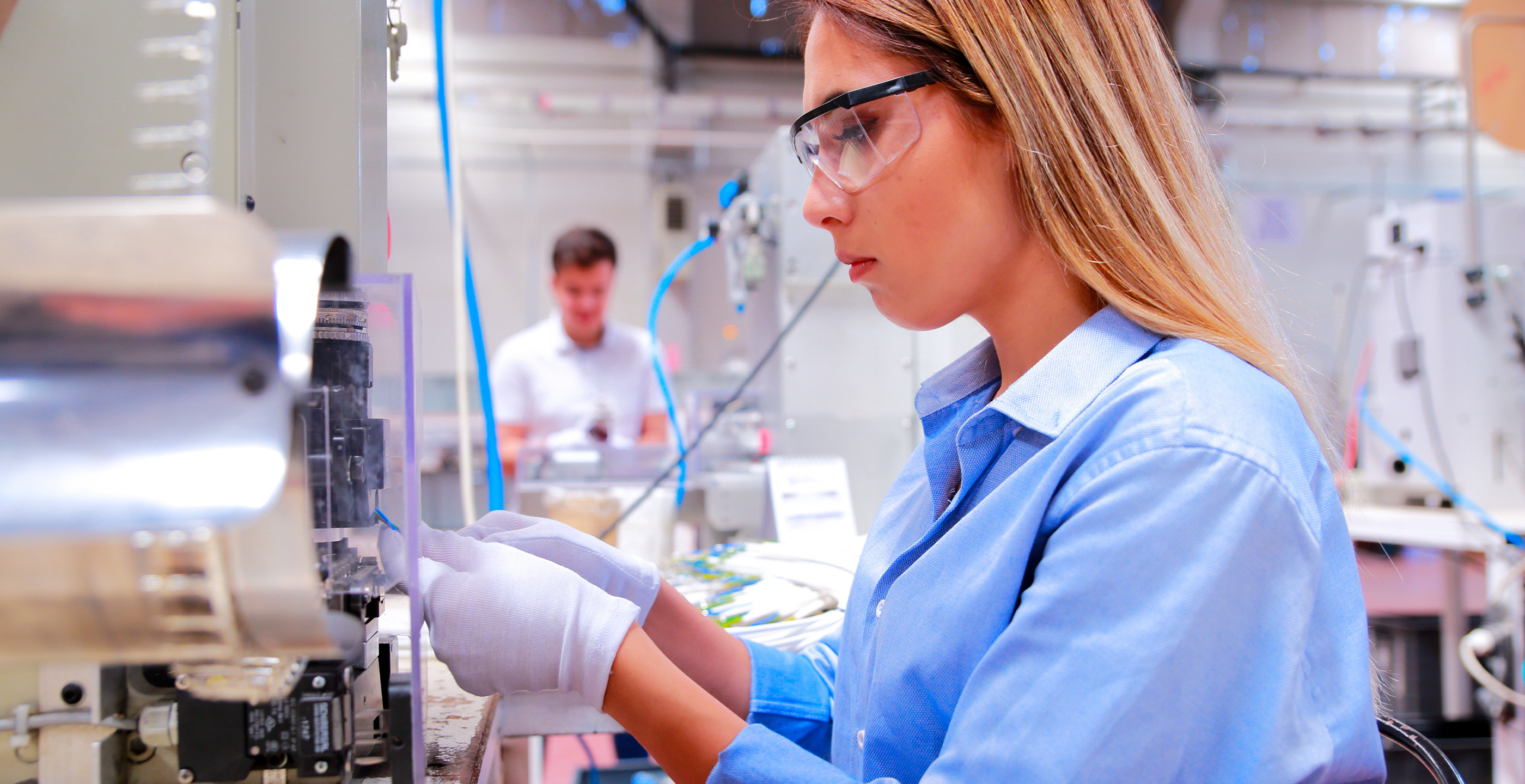
Manufacturers everywhere are adjusting to the new normal of the global supply chain. Not only are massive supply chain disruptions possible, but they can also happen at any time and affect any or every industry. Previously successful strategies such as just-in-time (JIT) inventory now only expose manufacturers to more risk, forcing them to shift from mass-scale production lines to smaller-scale lots of a few thousand units or less.
On the other hand, the conventional technologies of producing metal molds requires a significant up-front investment. This makes them less attractive for small-scale production, leaving manufacturers with an unpleasant choice: to absorb higher costs and reduce profit margins or pass costs to customers and risk losing market share.
Our team at Nagase ChemteX, a core manufacturer of the NAGASE Group, has developed and produced a solution that provides mold manufacturers with a better option—the ability to quickly create low-cost custom molds using a 3D printer and our high-heat-resistant optical molding resin.
The Challenge: Low-Cost Molds with Less Lead Time
Typically, mold manufacturers and parts manufacturers that make molds in-house utilize metal molds made of carbon steel or stainless steel. While these molds are robust solutions, the relatively high cost of producing metal molds can only be justified if they’re used to produce components and parts at scale—usually tens of thousands of units or more. In the case of parts that only need to be produced infrequently, this has historically meant keeping and storing molds for indefinite periods of time.
At the same time, customers are increasingly demanding shorter development lead times, and more mold manufacturers are seeking solutions to produce more dies in shorter times and at lower costs.
The Solution: RHRCM-Series Resin
Nagase ChemteX has developed a resin known as the RHRCM-series resin. By using our own formulation and dispersing technology, we produced a resin that offers customers the perfect balance between heat resistance and cost-effectiveness.
Compared to metal molds produced from CNC or wire-electrical discharge methods, 3D-printed molds made from RHRCM-series resin are much less costly to manufacture. This makes our molds perfect for smaller-scale production of parts—on the order of hundreds or thousands of parts rather than tens or hundreds of thousands—when the higher cost of a metal mold is harder to justify in this context. At the same time, our RHRCM-series resin offers heat resistance of 250°C (480°F) or higher, which can withstand molding of most engineering plastics.
The Process: From Customer Need to NAGASE Solutions
We work with mold manufacturers worldwide, providing solutions to each customer’s specific mold requirements.
First, our team reviews a digital 3D computer-aided design (CAD) file created by you so that we can better understand the technical requirements of your mold. Then, we discuss the commercial requirements with you, including the expected timeline and production volume.
You can even visit a workshop to do prototyping with our team. For example, we work with EMPOWR3D™, an innovation center in the US that provides customization of materials, printer tuning, and testing to ensure optimal performance.
We’ll help you select the best resin from our existing product line for one-off and low-volume mold production. For high-volume applications, our experts at Nagase ChemteX can develop a fully customized resin tailored to your specifications.
Once the mold resin is produced, it is shipped to your facility, where your mold can be 3D-printed on-site.
Verification: A Truly Versatile Mold Resin
Our team of experts at Nagase ChemteX has tested our heat-resistant resin in a wide variety of injection molding applications using 3D printer stereolithography (SLA). The RHRCM-series resin is compatible with the most widely used general-purpose and engineering plastics, including:
- Polypropylene (PP)
- Polyethylene (PE)
- Polystyrene (PS)
- Acrylonitrile butadiene styrene (ABS)
- Polycarbonate (PC)
- Polyethylene terephthalate (PET)
- Polybutylene terephthalate (PBT)
- Polyoxymethylene (POM)
Not only is our resin heat resistant over 250℃, but our resin also makes it possible to create a resin mold that can withstand injection molding. Our resin also makes it possible to consider alternatives to ceramic parts.
The resin molds can be printed on SLA printers, as well as DLP and other photopolymer printers. Additionally, they can be customized to meet customer needs.
Moving Forward
Today’s strained global supply chain has put manufacturers under more pressure to produce a greater volume of products in less time and at a lower cost.
Using our heat-resistant resin in your 3D printer, you can create molds and be prepared to meet your customers’ present and future demands. This means you no longer have to store molds for indefinite periods of time and can quickly adapt to the needs of customers seeking highly specific after-parts. Creating your own molds is also much more cost-effective and allows for rapid prototyping, allowing you to innovate and adapt. Contact us to download a technical datasheet and learn more about our RHRCM-Series resin and how we can help you get started today.
*Product commercial availability may vary by country.
Related Resources
We’re Here to Help
Complete the following fields with your information, as well as a short, detailed description of your request and a NAGASE Specialist will be in touch with you shortly.