Solving Chemical Polishing Challenges in Metal Component Manufacturing
Manufacturers of automotive, aviation, electronic, and medical device components often rely on metal 3D printers and manufacturing equipment to process metal parts with complex shapes. However, processing metal parts via 3D printers often results in various irregularities inflicted on the surface of the metal, such as corrosion, scratches, and uneven surfaces. Because in standard methods, the metal powder is dissolved and then layered on, when the metal powder isn’t dissolved enough, it becomes uneven. In addition, due to the complexity of the components’ shapes, conventional polishing solutions have difficulty achieving a smooth finish.
One of our Group companies, Nagase ChemteX, recently set out to find the ideal chemical polishing solution to meet these challenges. Here’s how we identified manufacturers’ specific needs, our proposed solution, and the results of our work.
The Challenges
In the process of manufacturing components for automotive, aviation, electronic, and medical industries via 3D printing, much of the printing equipment used creates an uneven surface which is then prone to vulnerabilities.
Our team set out to identify the specific challenges this creates. In doing so, we determined we needed to solve all of the following issues:
- The burrs and scratches generated when processing metal parts and the surface irregularities of shaped objects produced via metal 3D printers are causing decreased performance, particularly regarding durability.
- Metal 3D printers can easily form complex shapes and internal hollow structures, but sometimes they produce shapes that cannot be polished by blasting or other conventional polishing methods. As such, the surface treatment work after forming the components requires time-consuming labor, resulting in an inefficient manufacturing process.
- Due to the unevenness of the metal surface, metal corrosion and cracking occur easily. This makes it necessary to flatten the outside and inside of the metal molding uniformly.
The Solution
To solve those challenges, our team proposed a liquid chemical polishing solution that would flatten metal surfaces that cannot be polished by hand. Our team was already putting this solution to use in the manufacturing process of semiconductors and displays. This solution has been used by our team to get rid of photoresists, perform etching, and scrape unnecessary parts off. We have been developing this chemical solution for 30 years, and we now set out to test this solution in a new way. Through this process, we aimed to achieve surface flattening while improving component durability.
The Results
By optimizing the formulation of chemical polishing solutions for various metal types, such as stainless steel (SUS), aluminum, titanium, and Inconel®, we reached the flatness of metal surfaces that our customers required. Not only that, but we learned that we could also successfully customize chemical polishing liquid for various metal types such as SUS, aluminum, titanium, and Inconel. Our solution uses multiple ingredients that we mix in-house. Because the way the chemicals are mixed impacts how they dissolve and that the characteristics of the metal differs, we create custom formulations based on the characteristics of the metal we're working with.
Through our process, we could uniformly planarize complex shapes such as lattices and internal structures that conventional physical polishing could not.
Additionally, since our process does not use physical force, it will not change the material, such as the processed surface layer. We work to flatten the surface and work on the planarization. Through our process, the surface is made even, but we don’t change the character of the material, and the functionality of the metal remains intact. Our approach is also superior in throughput as it can simultaneously process large amounts of data.
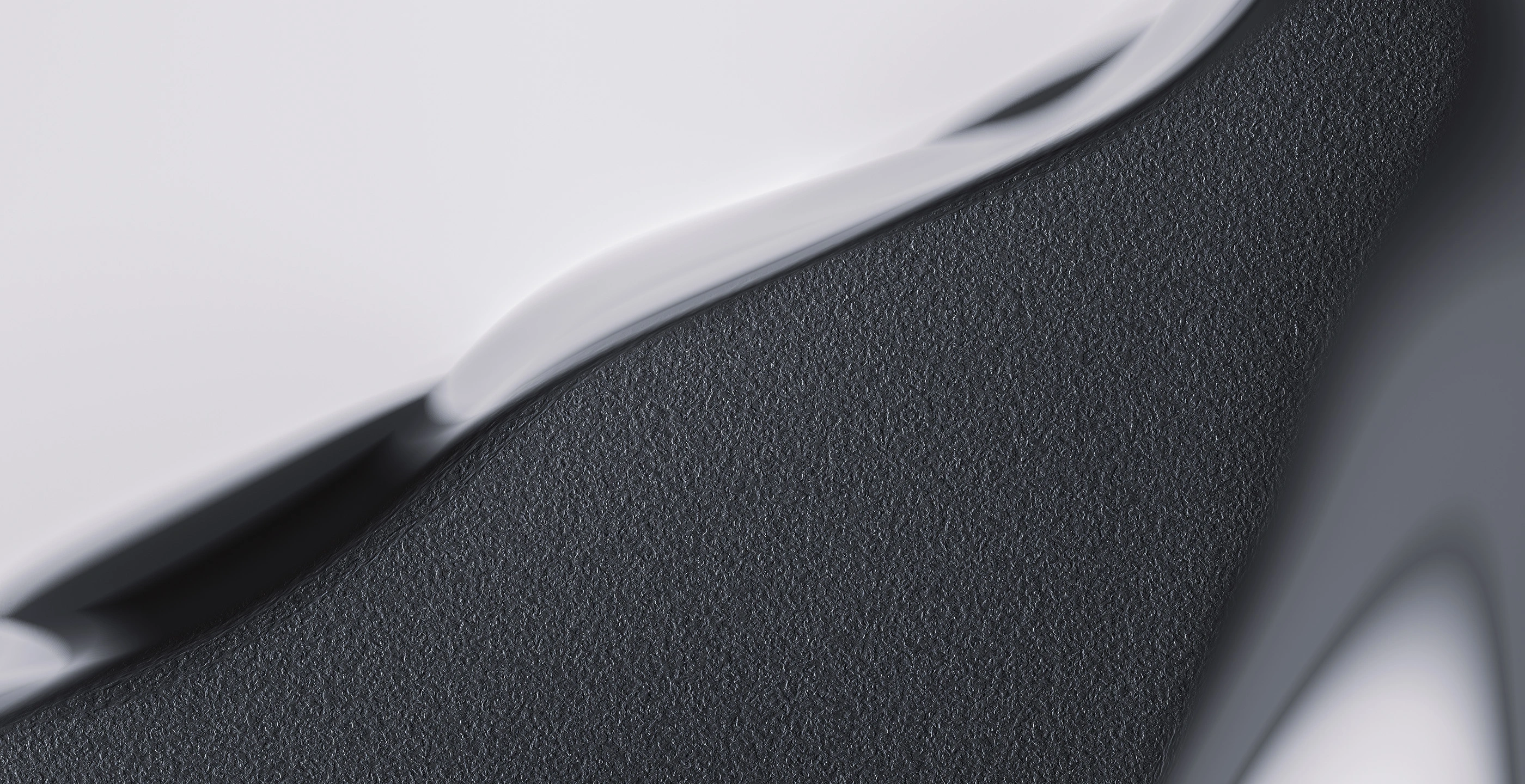
Looking Ahead
Our team has developed superior etching and anticorrosion technology through extensive work in the semiconductor and display industries. We can put this technology to use to help your team improve irregularities on metal surfaces via a chemical polishing solution. Please contact our team if you are interested in learning more about putting this solution to work in your manufacturing process.
We look forward to solving your complex polishing challenges with unique custom solutions.
Related Resources
We’re Here to Help
Complete the following fields with your information, as well as a short, detailed description of your request and a NAGASE Specialist will be in touch with you shortly.