Solving the Challenge of Removing Endotoxins
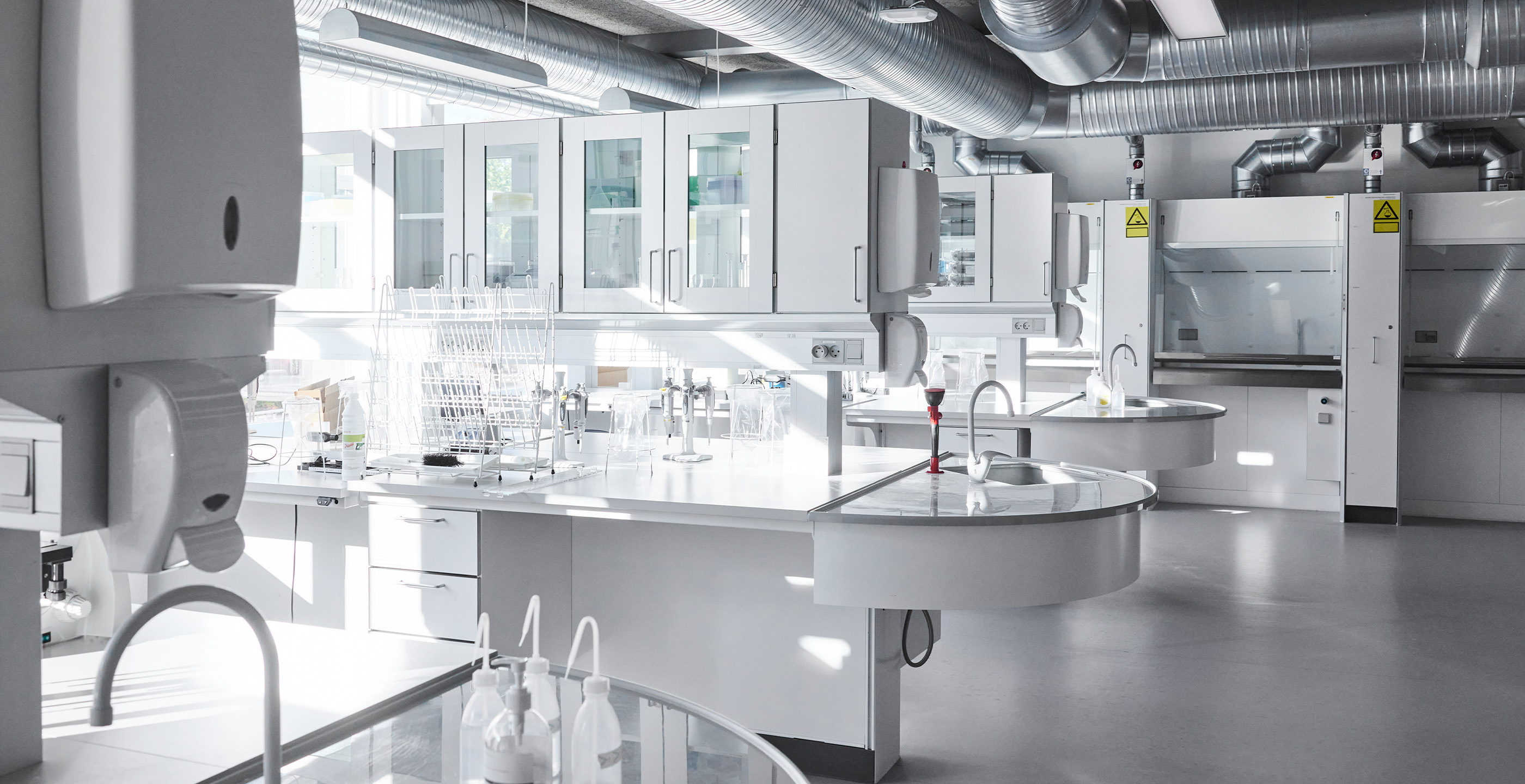
Since the first applications of biomaterials half a century ago, modern medicine has never been the same. Today, the development of advanced biomaterials, including smart biomaterials, has helped to bring about a new revolution in medical device design and manufacturing.
Biomaterials, which are synthetic materials used to restore function to body tissues, are more widely used than ever. Not only can they be formed into smaller and more complex shapes, but they can be easily mass-produced for patients worldwide. Artificial heart valves, tooth replacements, materials for contact lenses, and joint replacements are a few of the most common use cases for biomaterials.
These new opportunities have come with challenges, especially when minimizing endotoxins on novel or uncommon biomaterials.
Endotoxin Regulations in the United States
Regarding medical devices that contact the cardiovascular or lymphatic systems, the Food and Drug Administration (FDA) currently regulates the maximum acceptable level of endotoxins in medical devices at 0.5 endotoxin units per mL or 20 endotoxin units per device. The limits for devices that contact the cerebrospinal fluid are even lower at 0.06 endotoxin units per mL or 2.15 endotoxin units per device.
For medical device manufacturers, a product design risk can become a regulatory risk for challenging and novel biomaterials that do not comply with these safety requirements using conventional endotoxin removal methods. Without specialized endotoxin removal methods, the only choice is redesigning the device, costing valuable R&D time and money.
Winning the Fight to Remove Endotoxins
At NAGASE, we apply our endotoxin removal technique to help customers find the best solution for their specific product issues.
Nagase ChemteX, a core manufacturer of the NAGASE Group, has developed a line of endotoxin removal agents that utilize fine chemical organic synthesis technologies in collaboration with Kumamoto University.
It can be challenging to develop a purification process to remove endotoxins and consistently obtain low-endotoxin materials. We offer endotoxin removal services for various materials from which endotoxins are especially difficult to remove. Alternatively, we can assist customers in selecting the best low-endotoxin materials directly from our catalog.
Solving Customer Challenges
A medical device manufacturer came to NAGASE looking for help with a particularly challenging project. They were developing a new device that incorporated multiple biomaterials, some of which had high endotoxin concentrations.
While the company’s R&D lead understood the need to remove endotoxins from these biomaterials before incorporating them into their products, they were unsure of the most efficient way to do so.
To help this client produce a safe product and get it quickly to market, we adopted a multi-step solution that has helped other medical device makers with similar challenges.
Offering Real Solutions
Our team began with a tailored proposal that allowed the customer to choose between two viable solutions.
Solution 1: Select from the existing NAGASE product lineup of low-endotoxin materials. The customer would be advised by our expert team of product engineers and would be able to customize specifications as needed. This approach often meets the needs of our clients while reducing overall production time.
Solution 2: Design a customized endotoxin removal service, which would include endotoxin removal studies as well as removal services for materials for which it’s challenging to achieve low-endotoxin levels consistently. This is often the best approach for clients developing highly specialized or novel equipment.
Our services also include commercialization support as needed.
Survey & Analysis
Depending on the best solution for your application, the next step is to survey, test, and analyze the material(s) of interest.
Solution 1: For low-endotoxin materials selected from our catalog, we can provide material samples for you to proceed to the first evaluation.
Solution 2: For a fully customized endotoxin removal service, we will first confirm the details of the endotoxin removal study, execute any required NDAs/confidentiality agreements, exchange necessary information, and provide a study estimate before conducting the study and reporting back on the results.
Hypothesis & Verification
After initial testing and studies, we will arrange a formal discussion to address any reactions, questions, and concerns before moving to the final stage.
Solution 1: After you’ve had the opportunity to evaluate our product sample, you’ll be able to further customize the product specifications for your final product design.
Solution 2: After discussing the results of our endotoxin removal studies, we can prepare a sample of your customized low-endotoxin materials for first evaluation and fine-tuning.
Final Proposal
Once the low-endotoxin material has been designed, produced, and shipped, our specialists will continue to fully support the development of your new product through the commercialization stage.
Moving Forward
Companies everywhere constantly push the boundaries of improving lives with new materials and new ways to use known materials. When they face problems related to removing endotoxins, they turn to NAGASE to develop a low-endotoxin solution for their devices.
For life science-related companies such as medical devices, pharmaceutical companies, and regenerative medicine, don’t hesitate to get in touch with us to see how we can work together to find the right low-endotoxin solution for you.
Related Resources
We’re Here to Help
Complete the following fields with your information, as well as a short, detailed description of your request and a NAGASE Specialist will be in touch with you shortly.